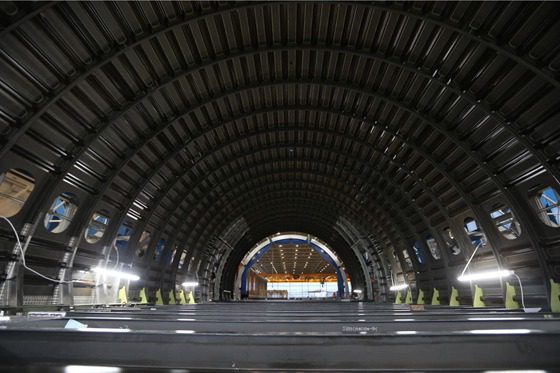
W020190108385108925384
Future airliners could have even lighter composite structures if new lessons on structural health data are applied. Current aircraft like the Boeing 787 or Airbus A350 are ‘structurally overdesigned’ and their successors could lose weight without compromising structural integrity, the first results of a test campaign by Technical University Delft (The Netherlands) and Patras University (Greece) have learned. The results were presented recently to the media. How to make composite airliners even lighter.
The Aerospace Structures & Materials Laboratory of Aerospace Engineering Faculty of TU Delft and the Department of Mechanical Engineering & Aeronautics of the University of Patras have participated in a project called ReMAP since June 2018. ReMAP stands for Real-time Condition-based Maintenance for Adaptive Aircraft Maintenance Planning. The objective is to make maintenance of aircraft smarter and more fact-driven by using data from a new structural health monitoring (SHM) database.
“In the present situation, aircraft are maintained according to fixed intervals or in a reactive manner when something fails for non-critical systems. These are human-based decisions. The goal of ReMAP is to change this to adaptive condition-based interventions. We adapt our maintenance plans according to new information that is available”, says project leader Bruno Santos of Delft Technical University.
“How do we do this? We facilitate the interchange of data coming from sensors and algorithms in terms of prognostics and diagnostics. For this, we have been developing an open artificial intelligence (AI) platform to share all this data in the cloud”, says Santos. “And we are developing sensing technologies and data-driven algorithms to monitor the health of structural elements of an aircraft.”
Current-generation composite airliners like the Boeing 787 are structurally overdesigned, the ReMAP team says. (Boeing)
Bruno Santos continues: “In parallel, we do the same thing for systems and there we not only use a data-driven but also a physics-based approach to help us understand better the root cause of failure of certain systems. Here, we also look at prognostics to determine the useful life of these parts. When we put together the prognostics and diagnostics from the structural elements and systems, then we can feed this into a maintenance scheduler algorithm that will tell when we should do maintenance on the remaining useful life of the structures and systems that we are monitoring.”
Of course, condition health monitoring isn’t new to the aerospace industry. Take Rolls-Royce or other engine makers, who with their “Intelligent Engine” or similar monitoring systems ‘read’ their engines in real-time conditions. OEM’s do the same, like Airbus with SkyWise which produces terabytes of data per flight and gives the airframer and airlines important information on the life-cycle of the aircraft.
ReMAP looks at lighter aircraft structures
What is different with ReMAP is that it also looks at (composite) aircraft structures like wings, flaps, the wing box, or the fuselage. Right now, structures don’t have sensors but a future generation of aircraft will surely need to have them for structural health monitoring in the way ReMAP is envisaging.
When an aircraft is hit now by, for example, a hail storm, the structure is usually checked visibly for any damage. While composites are durable, a direct hit by a foreign object could cause internal damage that might be left undetected and long term could cause problems. With sensors on them, structures can be monitored more carefully.
A laboratory setting at TU Delft of a composite structure equipped with numerous sensors to monitor stress. (TU Delft)
In laboratory settings in Delft and Patras, the ReMAP team has been testing composite structures representative of a wing structure that is fitted with dozens of little sensors. In various simulations, these structures were being put under all kinds of stresses while at the same time being monitored. In one test, hailstones were fired at a composite plate (designed by Embraer) using a gas gun.
“No damage was visible except for a small dent. You need additional light or feel with your finger where the dent is. This would be a big challenge in maintenance to detect it”, says Nan Yue, one of the researchers on the team. Agnes Broer, another researcher from the team adds: “With five sensing technologies, we are aiming to monitor the damage and see if it is growing under various tests and with prognostics how long this structure will last.” During the lab test, the structure was loaded up to failure. All information is fed into the Dataverse database with five sensing technologies that can be applied to multiple aircraft structures.
Sensor reliability needs more development
A problem that needs to be addressed is the reliability of the sensors on structures, says Dimitrios Zarouchas Assistant Professor of Artificial Intelligence for Structures, Prognostics & Health Management at TU Delft. “Reliability and the certification of sensors. As we showed in a picture, all sensors have wires that need to be certified.” Other research groups around the world are looking at the reliability of sensors, so Zarouchas is optimistic this will be solved.
Find the dent: during the 2018 Farnborough Airshow, the nose of the Mitsubishi MRJ90 was dented during ground handling. The damage was minor but was also almost invisible to the naked eye. (Richard Schuurman)
Access to data from KLM
For the predictability of systems, the ReMAP team already has had access to data from KLM’s Boeing 737 and 787 fleet. A real-time adaptive maintenance planning tool will be tested with KLM from September onwards for a six-month period. “What we already observe from preliminary results is that it is not possible for all systems to have a reliable health-monitoring solution. That’s because the sensors that are attached to systems are not necessarily there for health monitoring but more for control”, says Santos. Once fully developed, database-driven maintenance could save airlines in Europe some €700 million in costs, the research team thinks.
Long-term, Santos and his team see huge opportunities for additional cost savings as aircraft can be designed to different standards. “If we can monitor health conditions in a reliable way, then we can exploit the full life of our systems and structures, reducing costs without compromising safety. In the long-term, if we have such a system we can be less demanding on our design criteria for aircraft and have lighter aircraft flying”, says Santos. So this is the way how to make composite airliners even lighter.
Dimitrios Zarouchas adds: “We know aircraft are structurally overdesigned in terms of weight, especially the Boeing 787 but also the Airbus A350. If we manage to predict reliably and know when a part will fail and how it will fail, we can aim for lighter structures.” He thinks that structural components could be three to seven percent lighter. In the long term, the ReMAP team thinks that the adoption of a more efficient aerostructures design will result in a weight reduction of 10-20 percent. This translates into 105 tons less fuel and 350 tons of carbon dioxide emission reduction for an aircraft flying 700 flights per year.
The ReMAP and KLM will start a six-month trial to compare real-time data from systems on the Boeing 737 and 787-fleet with that learned during the project so far. (Richard Schuurman)
ReMAP has been funded with €6.8 million under the EU Horizon research and innovation program. It started in June 2018 and will conclude in May 2022, but the last year will be for demonstrating what has been developed. It has had the support of thirteen partners, including KLM, Embraer, Onera, ATOS, ENSAM, CEDRAT Technologies, Instituto Pedro Nunes, Optimal Solutions, Smartec, UTRC Ireland, and the universities in Delft and Patras.
EASA, Airbus, Thales, Collins Aerospace, and Embraer are a few names on the advisory board. “Airbus is looking at our program and following discussions as part of their advisory board membership. I don’t know how they look at it from the perspective of their business model, but we are sharing with them some of our decisions and results and are getting feedback from them”, says Bruno Santos.
He hopes the lessons learned from ReMAP will be picked up by a follow-on program, including the creation of a European academy where topics like SHM will be researched more. “We don’t do research for the sake of research, we do it because we want to see the practical benefits of that. That’s why it is important to work with the industry to have constant feedback.”
ReMAP will change aircraft maintenance
ReMAP is about making aircraft lighter and also changing the way maintenance is done. Bruno Santos tries to look ahead fifteen to twenty years into the future: “What we foresee for systems and structures is that aircraft will be flying with sensors, will land and communicate data from these sensors. From that, we will learn about all aircraft in the fleet what is the health condition of all the systems and structures. This information will be automatically fed into a maintenance scheduler that will propose a maintenance schedule to the decision-maker at the airline”
This is not enough, Santos adds: “To be reliable, we need to have the scope of multiple airlines. We cannot only rely on monitoring aircraft from KLM, but also from Lufthansa or British Airways. To do that, we are developing a federated learning approach in which we have algorithms being trained in multiple nodes which are the airlines. These algorithms are exchanged between airlines and the data stays at the airline node. In this way, we believe we will obtain the reliability needed to make condition-based maintenance possible.”
Views: 10