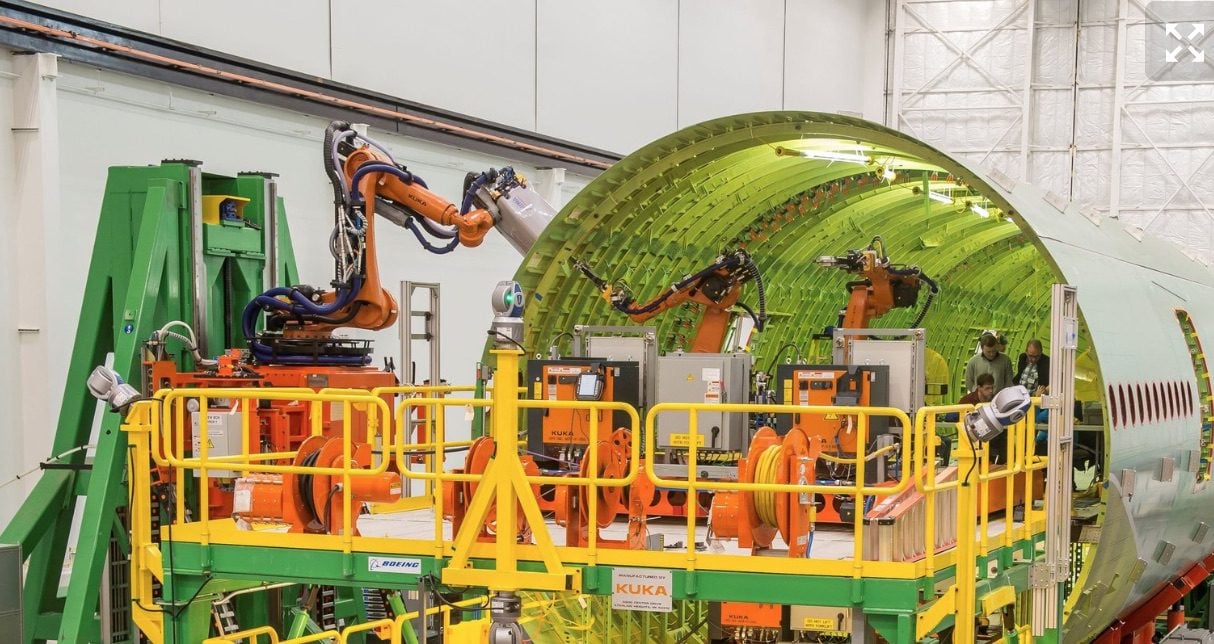
777 Robotics
Boeing has scrapped its robotic system that assembled two main fuselage sections for the 777 and forthcoming 777X. The company has struggled with this automated system for years and has pulled the plug, returning to human labor again to assemble fuselage sections.
Apparently the robots, which worked inside and outside the fuselage to drill holes and secure fasteners, could not synchronize holes properly, leading to substantial catch-up work that had to be finished by human intervention.
The system, designated FAUB for Fuselage Automated Upright Build, has had problems as far back as 2016, resulting in substantial rework and has been describes as “a horrible failure” in press reports.
Boeing will now utilize a less automated system called Flextrack that will pre-drill holes into which skilled labor will manually insert fasteners into the pre-drilled and countersunk holes.
Boeing’s automation strategy for 777X over-promised and under-delivered. But there may be several reasons for abandoning this automation initiative at Boeing. First, Boeing is suffering some cash flow issues as a result of the 737 MAX and will need investment capital for the NMA that it might launch next year. The company would likely rather prefer to invest in an aircraft with a higher production rate than the 777X, which has not sold well and is likely not going to achieve the 8.3 per month rate of its predecessor. Second, it is often easier to automate processes for new aircraft rather than existing models, as the processes can be more easily integrated into an aircraft that is “designed for automation.” It may simply be that Boeing has made a decision of where it can obtain the best return for its automation spending, which is likely the NMA.
Meanwhile, Airbus, its major competitor, is making inroads with its new A320 family assembly line in Hamburg that focuses on the A321XLR. Airbus uses Flextrack to drill and countersink holes, Airbus robotic system utilizes twelve additional robots to install more than 3,000 fasteners per fuselage on an automated basis completing the fuselage joining.
Airbus has had about a five year head start over Boeing in its efforts to automate factories, and is also looking towards additional automation as it develops new products. The next generation of narrow-bodies in the 2030s will likely include new materials that benefit from automated processes. Aircraft development, which used to be only the design of the model and basic manufacturing, now includes automation and manufacturing design as an integral component of the design process – and is one reason that development timeframes have stretched from around 4-5 to 5-7 years for new aircraft.
Bottom Line
Airbus has gained an advantage in aircraft manufacturing automation over Boeing with respect to fuselage assembly. Airbus’ system is now operational, and increasing capacity for the popular A321 that are replacing the Boeing 757, while Boeing is reverting to manual processes for its upcoming 777X.
It is not clear yet how this decision will play out with its labor force. The news will embolden them and Boeing has a rough history with its labor relations.
Coming at a time when Boeing is under pressure with the MAX, this will likely be touted in the press as another Boeing failure, especially since the company had highly touted this system for efficiency and quality. But, as discussed above, market and financial consideration may have led Boeing’s commercial aircraft business unit to a logical conclusion amidst resource constraints. Sometimes, pulling the plug is the right thing to do, especially when costs may outweigh the benefits for a slow-selling product like 777X.
Views: 42