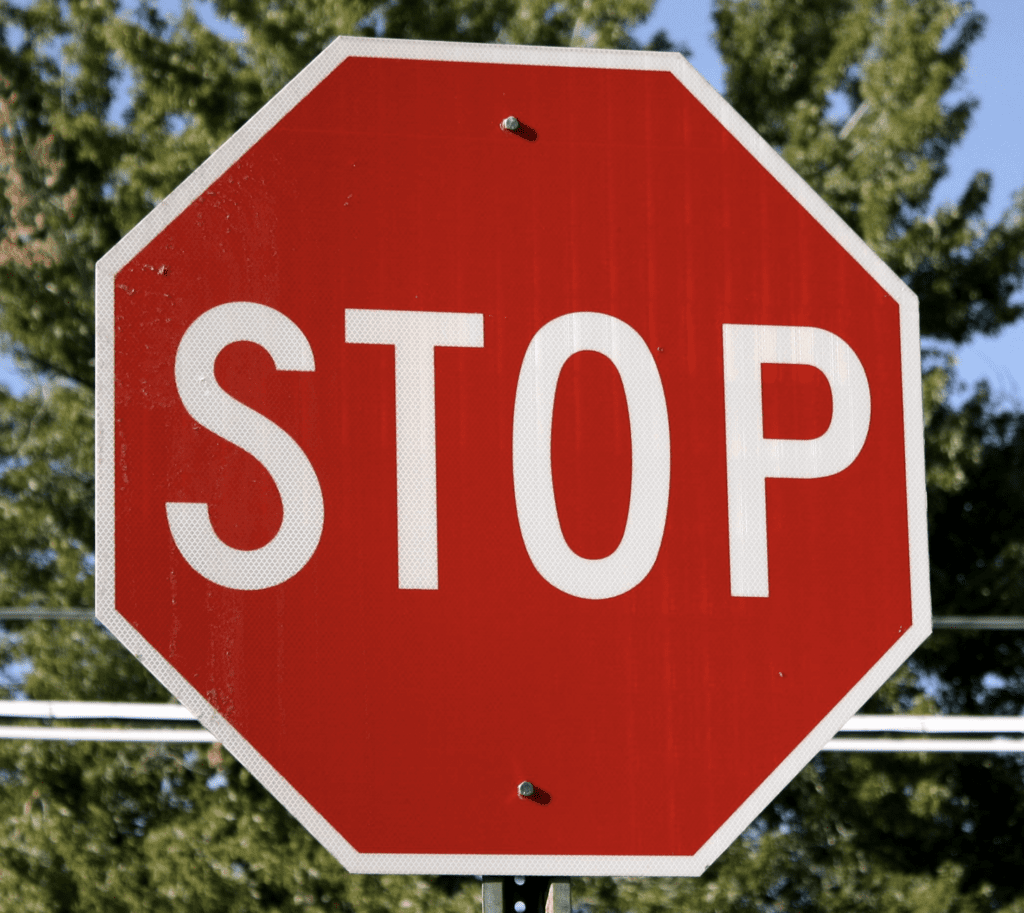
2024 02 12 143013
Airbus announced late last week that it will be late with some deliveries of aircraft in 2024, joining Boeing, where the FAA has prevented the company from increasing production rates as it investigates recurring quality issues. With record demand for today’s more fuel efficient aircraft, this couldn’t come at a worse time for the OEMs.
Since the onset of the global pandemic, the aerospace supply chain has been beset with multiple problems that are causing delays in deliveries of aircraft. The question OEMs like Airbus and Boeing face is whether this will get better in the near term. Unfortunately, the answer appears to be no for at least the first half of 2024, and likely not until mid-2025.
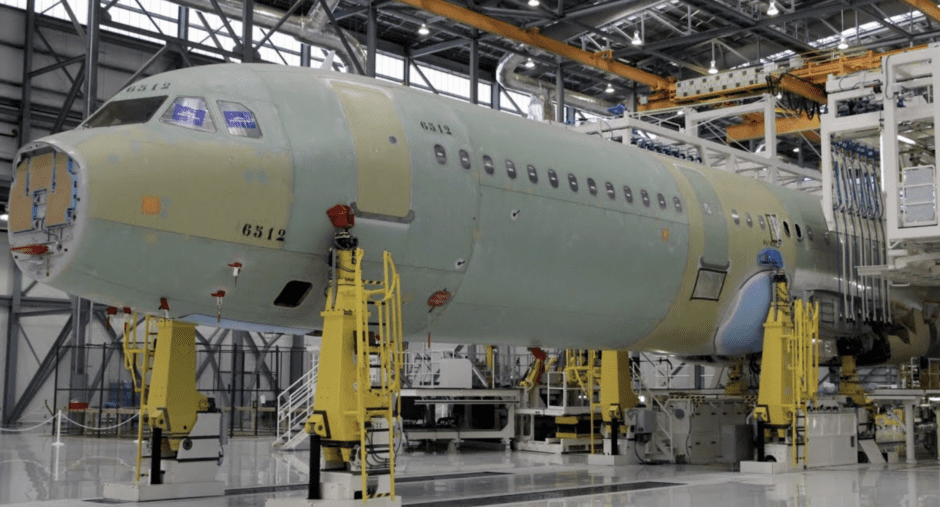
What Went Wrong
The production issues relate primarily to supply-chain employment, or more specifically, the lack of employees with the experience to maintain, if not grow, high production rates. In the wake of the global pandemic, many companies lost a significant number of employees to voluntary attrition. For many companies, the most senior, and also the most experienced employees, decided to retire early, accept contract buy-outs during layoffs, or simply leave the industry.
The result has been havoc for OEMs, who are struggling to increase production rates despite exceptionally high demand levels for new aircraft. They simply can’t produce the parts the OEMs have ordered on a timely basis. Since it only takes one missing part to hold up delivery of an airliner, there are thousands of opportunities for disruption with products as complex as airliners, which have an equally complex supply chain.
Compounding the issue are design, reliability, and supply issues with engines. These issues include the very popular Pratt & Whitney GTF and CFM International LEAP engines that power the latest generation of narrow-body aircraft and are in high demand. With a major retrofit due to a contaminated powdered metal issue with the GTF and constrained resources at Pratt & Whitney and other partner companies, Airbus faces a potential shortfall in engines for its best-selling A321neo models.
Ironically, a decrease in planned Boeing production mandated by the FAA may help Airbus as additional LEAP engines could become available as the engine companies struggle to keep up with planned production ramp-ups.
There is No Instant Fix
The lasting impacts of the pandemic remain visible in the aerospace supply chain, and while actions have been taken to improve the situation, their impacts are not immediate. From raw material shortfalls to limited production capacity for key specialties (e.g. investment grade castings) and a growing but inexperienced workforce still learning the trade, delays are to be expected.
Airbus warning of continuing delivery delays will have long lasting effects. With a 7-8 year backlog, demand continues to outstrip supply, and the book to bill ratio will likely be greater than 1 to 1 again in 2024. That means pushing something else back until production rates can be ramped to record levels to make-up the difference. But those planned rates have already been pared back in each of the last three years, and may also be adjusted for 2024 and 2025.
Another result of production shortfalls is inflation, both in component parts and in the market value of an aircraft. Whenever demand significantly exceeds supply, prices rise. This has occurred in raw materials, which have also been impact by geopolitical concerns for Titanium, with the largest producer in Russia. Inflation in material prices, combined with wage increases in a more competitive hiring market, is resulting in pressure on suppliers.
Since suppliers are contractually obligated to deliver at prices negotiated pre-pandemic to OEMs, it is difficult for suppliers to maintain production rates and quality. The prospect for a supplier losing money on every unit sold leads to other interventions. At the recent PNAA conference in Washington state, full of industry suppliers, the tone from Boeing changed from the hard-ball style of the last few years to a more conciliatory tone. It is clear that constrained suppliers are gaining the upper hand, after years of the OEMs in the driver’s seat.
What Can be Done
The answer, unfortunately, is to give things some time. As the multitude of newly hired employees gain experience, the situation will improve. The good news is that the industry has been hiring a strong rates, but the bad news is that it is often a two to three year process for employees to fully develop the skills they need for unsupervised work. We are perhaps 2/3rds of the way for many suppliers.
Improvement will continue, all the way through the supply chain, from raw materials suppliers to component fabricators to system integrators to the OEMs. The question is not if, but when, and what will it cost.
The Bottom Line
While we wait for corrective actions to take effect, airlines and leasing companies that planned for new aircraft will need to alter their fleet plans. New aircraft simply won’t be available on time. For some airlines and leasing companies, that means a six to nine month delay, or perhaps even a full year additional time to deliveries. That also likely means payments by the OEM if they exceed contractual delivery time frames, which often do include some slack time. But with a shortage of aircraft, air fares will remain higher than planned, impacting consumers. We don’t expect the supply chain to fully return to normal conditions until mid-2025.
Views: 33