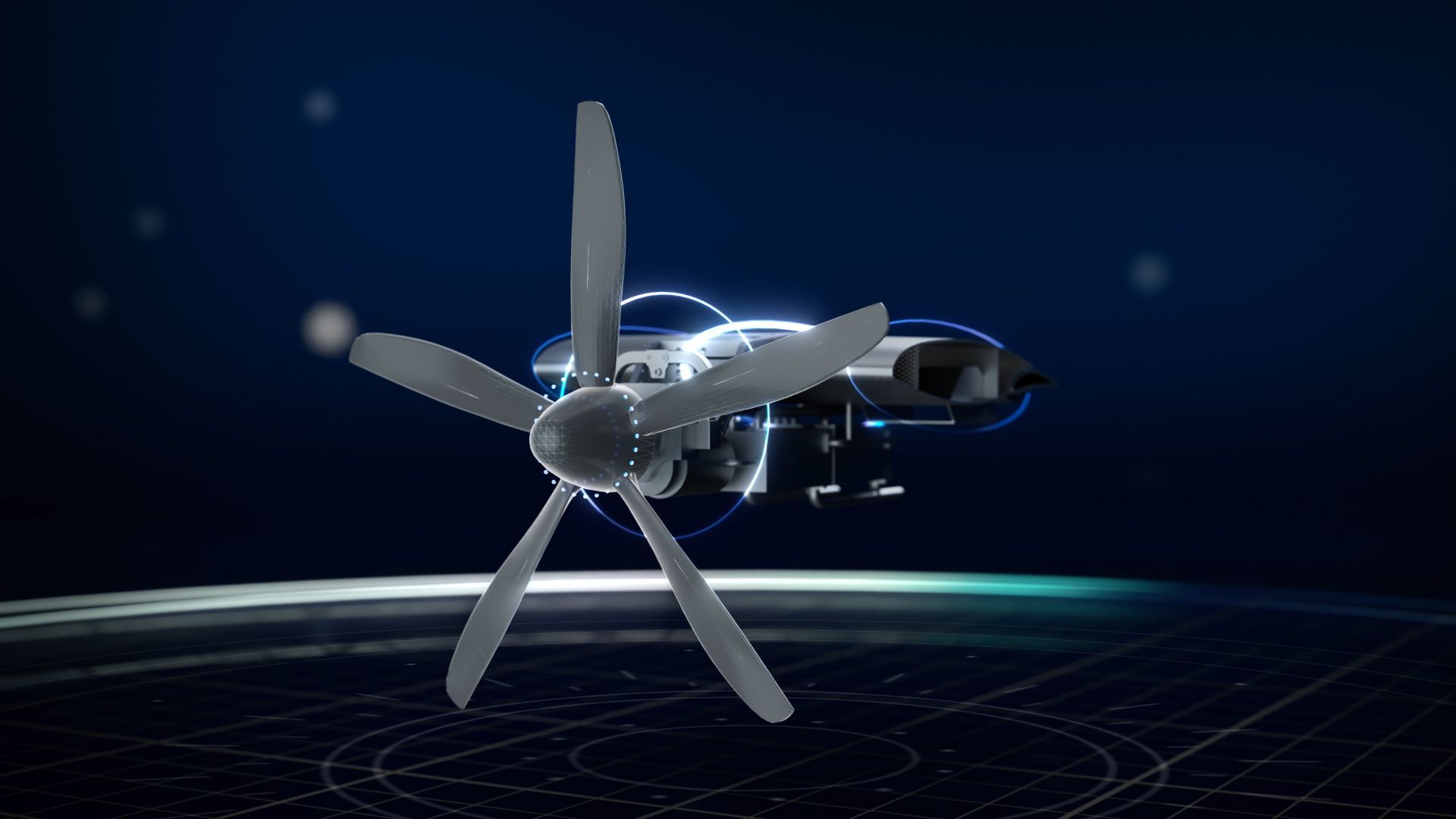
MTU FFC Propeller PAS 2023
MTU Aero Engines and MT Aerospace are jointly developing a liquid hydrogen fuel system for commercial aviation. The Flying Fuel Cell, which is on display at the Paris Airshow this week as a model, should enter service in 2035.
Germany’s MTU, which is doing a range of projects, has been developing a fuel cell system for years but said already last year that it had been getting into a higher gear. Now it confirmed that the joint development started already three years ago under the leadership of MTU. The first system will be ready for testing at its Augsburg facilities by the end of this year. It includes hydrogen tanks, sensors, heat exchangers, valves, plus safety and control systems.
Short shuttle and regional flights will be the first ones on which an aircraft with the FCC will be used, although MTU has yet to confirm a contract with an airframer. MTU says that as efficiency improves, it will then do short and medium-haul routes. “With some minor modifications, the LH2 fuel system that is currently being developed for the FFC could also be used for direct hydrogen combustion in aircraft engines,” says Barnaby Law, Chief Engineer Flying Fuel Cell for MTU, in a media statement.
In the work package between the two companies, MT Aerospace will cover the cryogenic hydrogen storage and supply system, additively manufactured heat exchangers, sensors, and system integration. MTU Aero Engines is responsible for the safety system, control system and valve technology. MTU has a team of around 100 engineers working on the FCC. All work is done in close collaboration with the European Union Aviation Safety Agency (EASA) in order to fulfill the certification and safety-related requirements.
“At MT Aerospace we have decades of expertise with hydrogen in the aerospace sector, and now we want to apply it to commercial aviation as well,” says Markus Staudt, Vice President and Head of Business Development Export, Defence & Hydrogen.
Electric motor
MTU is also working on other projects to achieve zero emissions. “Among other things, we are forging ahead with the full electrification of the powertrain,” explains MTU CEO Lars Wagner. “We’ve identified converting liquid hydrogen into electricity using a fuel cell as the area with the greatest potential for achieving this.”
A highly efficient electric motor for the MTU-FFC is being developed by eMoSys GmbH. The Starnberg-based electric motor developer and the small-volume manufacturer has been a part of MTU since April. Germany’s leading engine manufacturer is thus consistently expanding its know-how and activities relating to the electrification of the power train. The motor has a diameter of 30 centimeters, weighs 40 kilograms, and can produce 600 kilowatts of power with a performance density of 15 kilowatts per kilogram. The fluid-cooled motor can work at up to 85 degrees Celsius and it will also have multi-stack compatibility.
Once ground tests are complete, the system will be flight tested on a Dornier Do 228 of the German Aerospace Center DLR. The goal is to replace one of the two conventional gas turbine propulsion systems with a 600 kW electric powertrain with energy supplied by a hydrogen-powered fuel cell made by MTU and test the new configuration. The partners aim to launch the flying lab in the middle of this decade.
Views: 7