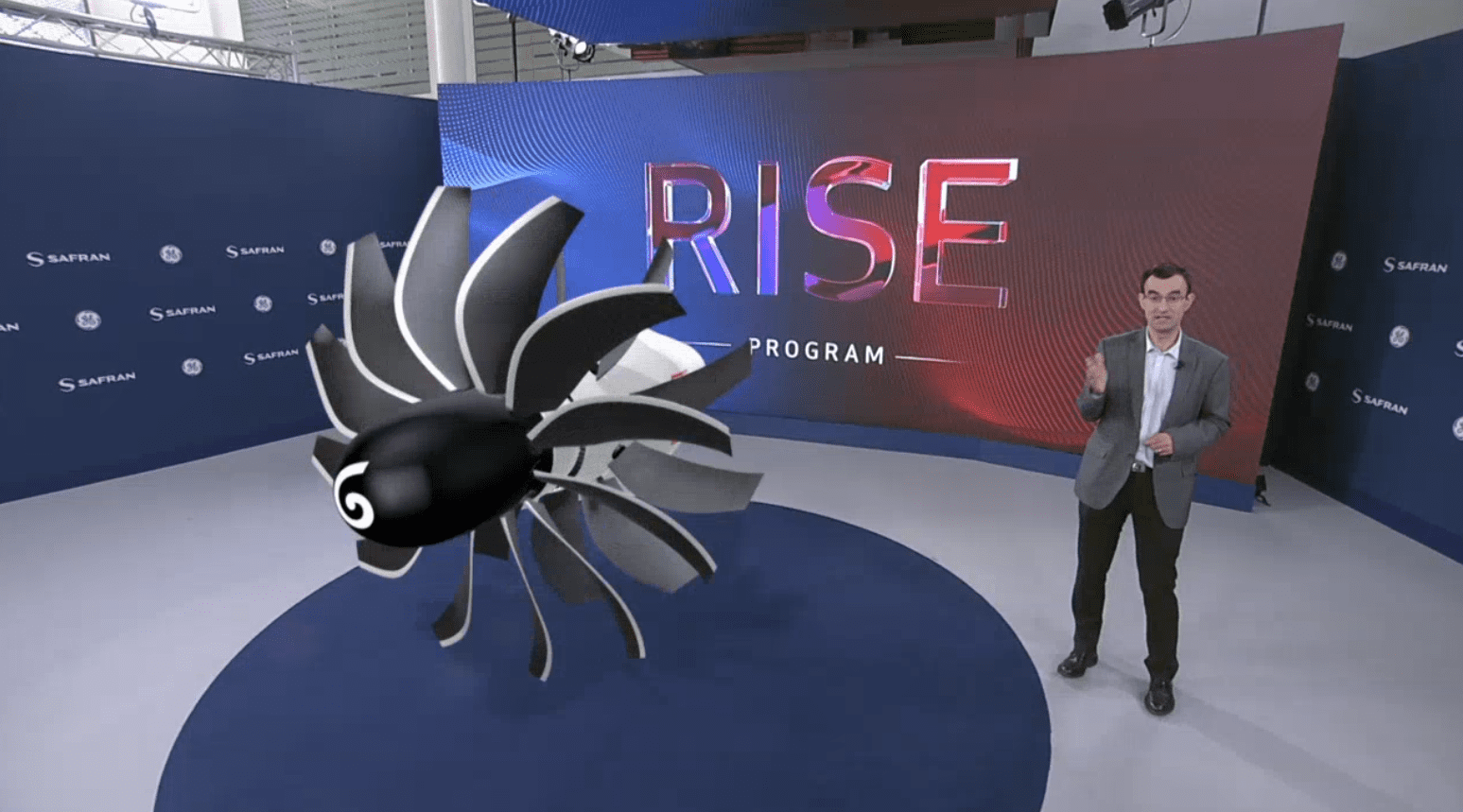
2021 06 14 1
They haven’t found a dedicated aircraft program yet, but General Electric and Safran are determined to have a new commercial aero-engine ready for entry into service by the mid-2030s. The engine should be over twenty percent more efficient than the most efficient current generation of engines, including their CFM LEAP, and reduce carbon dioxide emission by 80 to 100 percent. Interestingly, CFM commits to the open rotor with RISE program.
During an online event from Paris, GE President and CEO John Slattery and his Safran colleague Olivier Andries stressed that today isn’t the launch of a new engine program, but the start of a technology program that will lead to a successor of the LEAP. And as GE and CFM also have extended their partnership until 2050, the program is called CFM again, with the addition of RISE. Which stands for Revolutionary Innovation for Sustainable Engines.
Since starting their partnership in 1979, CFM engines have come a long way as far as efficiency is concerned. Fuel efficiency of the current generation of LEAPs is fifteen percent better over the previous CFM 56-7-family, or a combined forty-percent improvement over the CFM-2. But if the aviation industry wants to commit to the targets set out in the 2015 Paris Climate Agreement, engines have to go another big step. The answer to that is CFM RISE.
Open rotor has a long history
GE and CFM are the first to commit to a technological concept that, if really introduced, is disruptive to the industry: the open rotor. It has been tried and tested before by both OEMs, of course, but never entered a commercial program. GE developed the GE36 Unducted Fan (UDF) or propfans that first flew on a Boeing 727 in 1986 and on a McDonnell-Douglas MD80 in 1988. It never came beyond the testing phase after concerns over noise pollution, while lower fuel prices in the early eighties compared to the late seventies made it impossible to justify the development costs.
Safran was a partner on the UDF and continued developing the open rotor design on the Counter-Rotating Open Rotor (CROR). Under the European Clean Sky Sage-2 Open Rotor program, a demonstrator performed ground tests in October 2017. Although not mature, the program confirmed that a thirty improvement in fuel efficiency and CO2 reductions is possible. Safran and GE have applied for new funding under the EU Clean Aviation program that runs until 2028.
Safran tested the counter-rotating open rotor engine in Istres in October 2017. (Safran)
Behind the scenes, GE and Safran have continued development of the concept and completed several rig tests since 2019 until the official launch of the CFM RISE program today. Both companies have made available a combined 1.000 engineers to the program, Slattery said. According to GE’s Vice President of Engineering, Mohamed Ali, the program should result in “the single largest improvement in fuel burn ever made.” Not only should the engine be twenty percent be more efficient, but the integration of the engine and the aircraft could also bring an advantage of thirty percent, said Safran’s Vice President of Engineering, Francois Bastin.
Three key areas need further development
So CFM commits to the open rotor with RISE program. But before these targets are met, CFM RISE has a long list to complete. Arjan Hegeman, General Manager for advanced technologies, identified three areas that will have to be worked on: different architectures, materials, and hybrid-electrification.
On the architecture, RISE is looking at various options, but the most ambitious and most favored by both engine makers is the double open rotor. But don’t be fooled: only a single rotor is rotating, the other row of blades behind the rotating one is static. Mohamed Ali said this solution is the preferred one: “Both GE and Safran have been gaining multiple experiences with this architecture, starting all the way back to the eighties. We recently have also been able to use these learnings in rigs in addition to tremendous capacity in computational power. Now we have been able to actually make it a single fan. That not only reduces weight and complexity, it also opens up efficiency.”
RISE will have to meet stringent noise regulations, a problem on the UDF, and any turboprop flying out there. John Slattery stressed that as far as cabin and exterior noise levels of RISE are concerned, “there will be no degradation to the comfort levels of the LEAP.” Andries added that noise at airports will be at identical levels to the LEAP. Helping to reduce noise from the rotors will be a powered gearbox.
Comprehensive roadmap on material development
On materials, GE and Safran say they have laid out a comprehensive roadmap to develop the most durable composite fan blades. Whereas the LEAP and GE’s GE9X already use parts from new allows, ceramic matrix composites, and 3D-printed parts, the engineers will expand their research for even newer and more durable alloys that will allow the engine to operate more efficiently from a thermal and propulsive perspective. For instance, it will have a compact core with very high compressor pressure ratios and a higher speed booster. A waste-heat recovery system will reduce emissions.
The third area that needs further research is fuels and hybrid-electrification. From the start, RISE will be designed to run on 100-percent sustainable aviation fuels (SAF), which would reduce CO2 emissions by eighty percent. The engine will also be compatible with hydrogen, which would reduce emissions by 100 percent.
The engine will also be able to fly on hybrid-electric energy, where the rotors are propelled by an electric motor that runs on electricity that is provided by a generator. This will provide additional power and generate electricity for use elsewhere in the aircraft. RISE should be the first to bring hybrid-electric technology to single-aisle airliners.
Three concepts for aircraft installation
How to position an open rotor on an aircraft? Francois Bastin showed three concepts. The first is the one seen before on the UDF and other open rotor designs, so with the engines mounted aft on the fuselage. Alternatively, they would fit a high-wing aircraft like the concept used for many years on the Fokker Friendship/F50, Bombardier/De Havilland Canada Dash 8-family, of the ATR. Or on the truss-beam wing concept that has been studied since 2014 by NASA and Boeing and recently was featured in NASA’s 2022 research program.
A RISE-engine could also be positioned under the wings of a low-wing aircraft, Bastin said. The installation would be challenging as the 3.9 meter rotors need sufficient ground clearance.
Olivier Andries said that RISE doesn’t target a specific aircraft program, although the engine could be an ideal candidate for the hydrogen-based airliner that Airbus is developing under its ZEROe program. “We have engaged with Airbus and Boeing on the project and they are really interested in the efficiency gains it brings. The open rotor concept is recognized as offering them this kind of fuel burn reduction.” “Technologically, it could be applied to any kind of aircraft architecture. The launch and configuration are up to the airframer”, said Slattery.
Asked if he would like to join Boeing if it is ready to launch a new program, Slattery said that “if Boeing offers a platform, we will compete, we will be eager to get on board.” He also encouraged Pratt & Whitney and Rolls-Royce to engage on the same open rotor concept: “Bring your best engineers, search the best technologies, let us compete! Ultimately, the planet would be the beneficiary. I welcome competition, let’s go for it.”
First tests not expected until the mid-2020s
The schedule for RISE includes over 300 component, module, and full engine builds, with the first ground tests not expected until the mid-2020s. Flight testing on GE’s Boeing 747 flying testbed should follow in the second half of this decade, with an entry into service in the mid-2030s. That wholly depends on what Airbus and Boeing have in mind, but also on the support from governments and other industry stakeholders. Slattery said he would like to have financial support from governments as well as their input on regulations, while airports need to offer the infrastructure for hybrid-electric and/or hydrogen-based aircraft. “This is an industry team sport. There is a big job ahead of us, but you can count on us.”
Safran’s Olivier Andries didn’t disclose how much his company is spending on RISE, except that it will be some 75 percent of its research and development budget. Slattery said that General Electric’s spending will be a significant part of its research budget. The US company will spend some $1.8 billion on R&D this year, about the same as last year. As Mohamed Ali said: “There will be learning, and maybe setbacks. But we are resolute and our objection very clear: inventing the future of flight and making it sustainable.”
Views: 99