
First A330neo delivery to Corsair scaled
Airbus PR — Since its first delivery in November 2018 and with over 120 aircraft in service today, the A330neo Family has already received various incremental improvements. These include a maximum take-off weight (MTOW) increase from its originally certified 242 metric tonnes to 251 tonnes; certification to ICAO’s 2028 CO2 emissions standard; higher “Max-Pax” capacity increase for the A330-900 from 440 to 460 seats in nine-abreast all-economy; as well as a Trent 7000 HP-turbine engine durability enhancement package from Rolls-Royce – doubling the in-service blade life for increased time-on-wing.
Continuing the A330neo’s evolution trend: From around Q4 2025, customers will be able to take delivery of an aircraft with even more operational performance and flexibility thanks to the next incremental package, referred to as “Step 4”. This will focus on enhancing the aircraft’s low-speed performance. This is achieved by further maximizing lift and reducing drag during the take-off and subsequent climb-out phases.
Airbus says Step 4 package A330-900 operators will benefit from an extra take-off-weight uplift capability of around 2.6 metric tonnes at some airports. At runway-restricted airports, the net gain could be as much as four tonnes – without increasing engine thrust. Airports where such operators could expect gains include Madrid, Minneapolis, Reunion, Dusseldorf, Bogota, Gatwick, and Mumbai. This program is steadily gaining customers.
They point out that two main enablers achieve drag reduction and lift improvement together. The first is the provision of intermediate flap settings, known as ‘Enhanced Take-Off Configurations’ (ETOC). The second enabler is the implementation of faster landing gear + landing gear door retraction sequences. These are respectively described below.
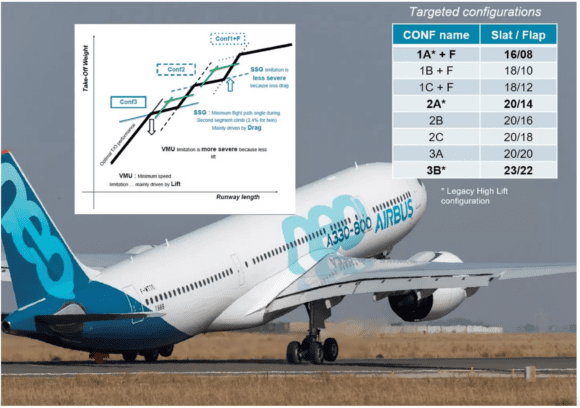
Airbus explains ETOC as follows: One needs to understand that today the A330 and A320 Families’ common-cockpit has five flap/slat lever settings: Flaps-0 being fully retracted, through positions -1, -2, -3, and finally ‘Full’.
On take-off, the flap setting depends on the available runway length and engine thrust settings – plus other factors such as second-segment climb obstacle clearance, etc. In general, the higher the flap setting, the greater the associated lift produced during take-off.
However, a higher flap setting also naturally creates more aerodynamic drag (which impacts the aircraft’s acceleration), especially during the initial climb phase. Therefore, a lower flap setting is usually preferred when runway length allows. Thus, “Flaps-Two” is a typical setting since it provides a good balance between the extra lift needed for take-off and lower drag for the subsequent accelerating climb-out whilst maintaining the required flight-path angle.
Airbus identified scope for further performance optimization and smoothing out flap and slat transitions by introducing intermediate ‘bridging’ flap positions – i.e., slotting between Flaps-One and Flaps-Two and between Flaps-Twp and Flaps-Three and Flaps-Full, respectively.
From next year, pilots of newly delivered A330-900s can enter the intermediate flap settings into the Multi-Function Control & Display Unit’s (MCDU) ‘Performance’ page. The four extra flap positions (in addition to the existing five flap lever settings) are denoted as 1B, 2B, 2C, and 3B. The particular take-off flap setting and corresponding take-off ‘V-speed’ values will be provided to the pilot by the EFB’s runway performance calculator app.
Once flap levers are set (e.g., to 1+F, -2, or -3), the aircraft’s avionics automatically move the slats and flaps to the desired intermediate position (e.g., Flaps-2A / 2B and so on) for take-off – as set already in the MCDU. For ETOC implementation, there are no physical changes to the flap lever itself. Some avionic computer hardware modifications, such as to the ‘Flight Management Guidance and Envelope Computer’ (FMGEC), are also required.
Shortening the landing gear retraction time by ~0.8 seconds and reducing the landing gear doors’ opening and closing time by ~0.2 seconds combined with these new settings are estimated to translate into one second saved, equalling one extra tonne of payload.
If one looks back over the history of the A330 program, it could be argued that the A330 is the most successful Airbus widebody produced. It has seen derivative after derivate with growing capabilities. It served as Airbus’ widebody freighter (not a great success) and a military version, MRTT, which has seen much more success. The A330ceo eclipsed the 767 in passenger service. The A330MRTT competes against the 767-based tanker. Now, the A330neo competes against the 787.
As we move into a period of derivatives rather than clean sheet designs, the A330 is proving to be a program with the potential to keep improving.
Views: 85