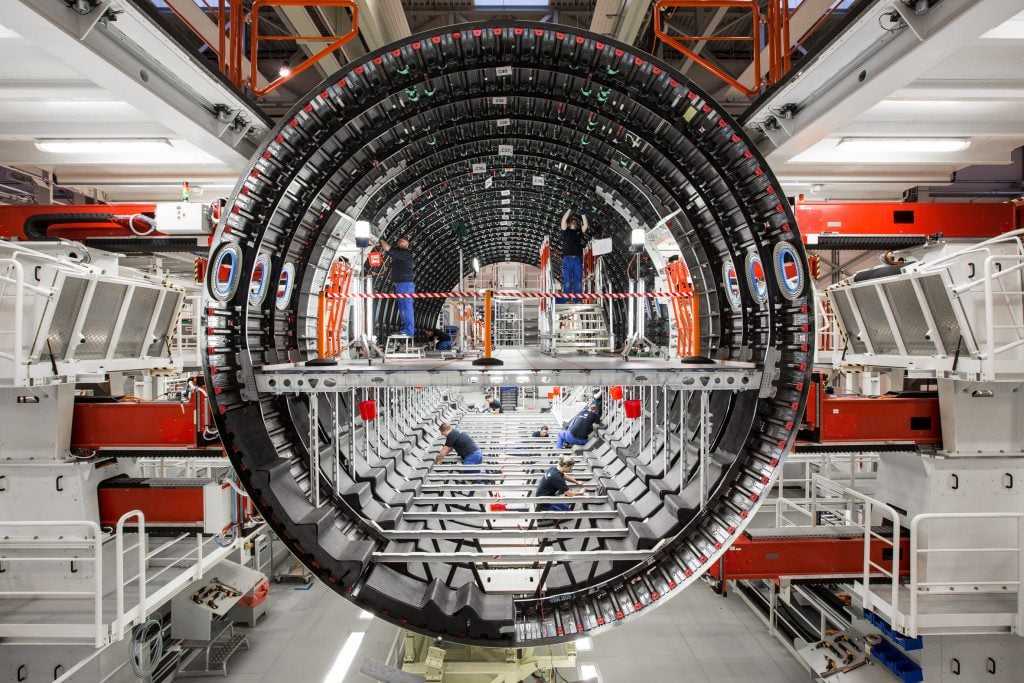
IMG 7675
Adapting the production system to make sure that Airbus is ready to ramp up the design and production of very complex and innovative products while maintaining the highest quality standards. That’s why Airbus fully integrates its aerostructure business. It will create three new entities, which should be ready from January 2022.
Detailed plans of the transformation were announced on April 21 after Airbus shared them during a European Works-Council meeting. However, it was during the 2020-results presentation on February 18 (see Airinsight) when President and CEO Guillaume Faury revealed that Airbus would rather keep its aerostructure subsidiaries Premium AEROTECin Germany and STELIA Aerospace in France rather than divesting of them.
The STELIA Aerospace Saint-Nazaire facility produces nose sections for all Airbus aircraft. This is an A350-1000 nose. (Airbus)
Airbus has provided Airinsight with additional information on the new business segment, which follows a thorough strategic review. Instead of just keeping Premium AEROTEC and STELIA Aerospace as separate companies, they will be fully integrated with other aerostructure activities.
In France, Airbus will integrate its Saint-Nazaire and Nantes sites with STELIA and its worldwide activities to form a new entity. STELIA has five sites in France in Toulouse, Saint-Nazaire, Rochefort, Meaulte, and Merignac as well as sites in Tunesia, Morocco, Portugal, and Canada. In Europe, the new entity will produce nose sections and central wing boxes for all Airbus family aircraft, the forward fuselage of the A320, and the central fuselage sections of the A330 and A350. In Canada, STELIA produces front and aft fuselage sections of the A220, parts for the A330, plus fuselage sections for the Bombardier Global 7500. STELIA also produces wings for ATR and the aft access ramp for the Airbus A400M as well as helicopter beams.
In Germany, Airbus Stade and Hamburg aerostructure activities will merge with Premium AEROTEC’s sites in Nordenham, Augsburg(I-III), and Bremen. The preferred ownership structure of the German activities is still under review. The German entity will continue to produce forward fuselage sections of the A330 and A350, centrale fuselage sections of the A320, aft fuselage plus aft tail cone sections, and vertical tail fins of all Airbus aircraft.
The impact of the transformation of aerostructures on staff numbers is yet unclear. This is Airbus Stade in Germany. (Airbus)
Airbus will also enter the Detail Parts market with a dedicated entity, combining the capabilities of the Premium AEROTEC plants at Augsburg (IV) and Brasov (Rumania) with Airbus Varel to produce parts and sub-assembly components for both civil and military applications. The new entity will have an initial volume of EUR 900 million. “This Detail Parts entity would have a comprehensive and consistent footprint in terms of assets, technologies, and skills to be fully autonomous.”
Stiff competition forces Airbus to reduce costs
The three new aerostructure companies will be wholly owned by Airbus and are no longer considered as suppliers but are a full part of the industrial complex. As Faury said in a speech to Airbus staff: “These organizations are intended to drive for competitiveness in the same way as other aerostructures tier-1 players: they would retain the flexibility to pursue speed, simplicity, and agility, as well as manage their own costs and deliver to benchmark quality.” Controlling costs is crucial: “We face competition not only from a resurgent, leaner Boeing but also new lower-cost manufacturers, notably COMAC and possibly others that have not yet emerged. We need to be well prepared for that.”
Airbus has also aerostructure businesses in Spain (Cadiz, horizontal tailplanes) and the UK (Broughton and Bristol, wings). On this, Airbus says: “They are already embedded in our value-stream management so there is no need to revisit them today. We are, however, currently assessing industrial operations in Spain from a workload perspective, following the impact of Covid-19 on widebody activity in particular, in addition to the end of A380 production.”
“Airbus continues to work with the social partners to identify solutions that will optimize the industrial set-up in the Cadiz area. We are working to secure capabilities for the long-term and prepare Airbus Spain to continue to play a strong role in Airbus’s future programs.”
Airbus hasn’t communicated in public what the impact will on staff numbers at the various sites: “Discussions with social partners have started and we will continue to work with them to prepare the ground, accompany employees that would be involved in the changes, and of course, ensure business continuity.” In February, the Airbus CEO confirmed that the company will have to its staff by 15.000, of which 6.700 had been furloughed by the end of December.
The challenges of designing and manufacturing a new generation of zero-emission, hydrogen-based aircraft play a major role in the transformation of the aerostructure business. (Airbus)
Don’t be fooled to think that the transformation is just a simple way to slash costs and reduce staff numbers. As Faury said in February and repeated on Wednesday, there is an urgent need to keep the aerostructure business fully connected to the design and assembly activities. “We believe, in light of the Company’s ambition to lead the decarbonization of our industry, that it is the right time to unite our industrial system into one digital design and production stream that flows smoothly towards the customer – to strengthen our “value stream”.
“Fuselage aerostructures are a central part of the Airbus value stream. Today, however, our activities in this field are fragmented across the company, our subsidiaries, and suppliers. Only by consolidating our core assets can we realize the full potential of “DDMS” (Digital Design, Manufacturing, and Services) and improve our ability to customize aircraft with less disruption to our production system. In doing so, we can reduce both lead times and cost.“
This is especially true as Airbus is at the first step of implementing a new product strategy that will focus on a zero-emission generation of aircraft based on hydrogen as the source of fuel. This requires new designs and new technologies, for which it is essential to have the knowledge and production capabilities in-house.
Views: 48