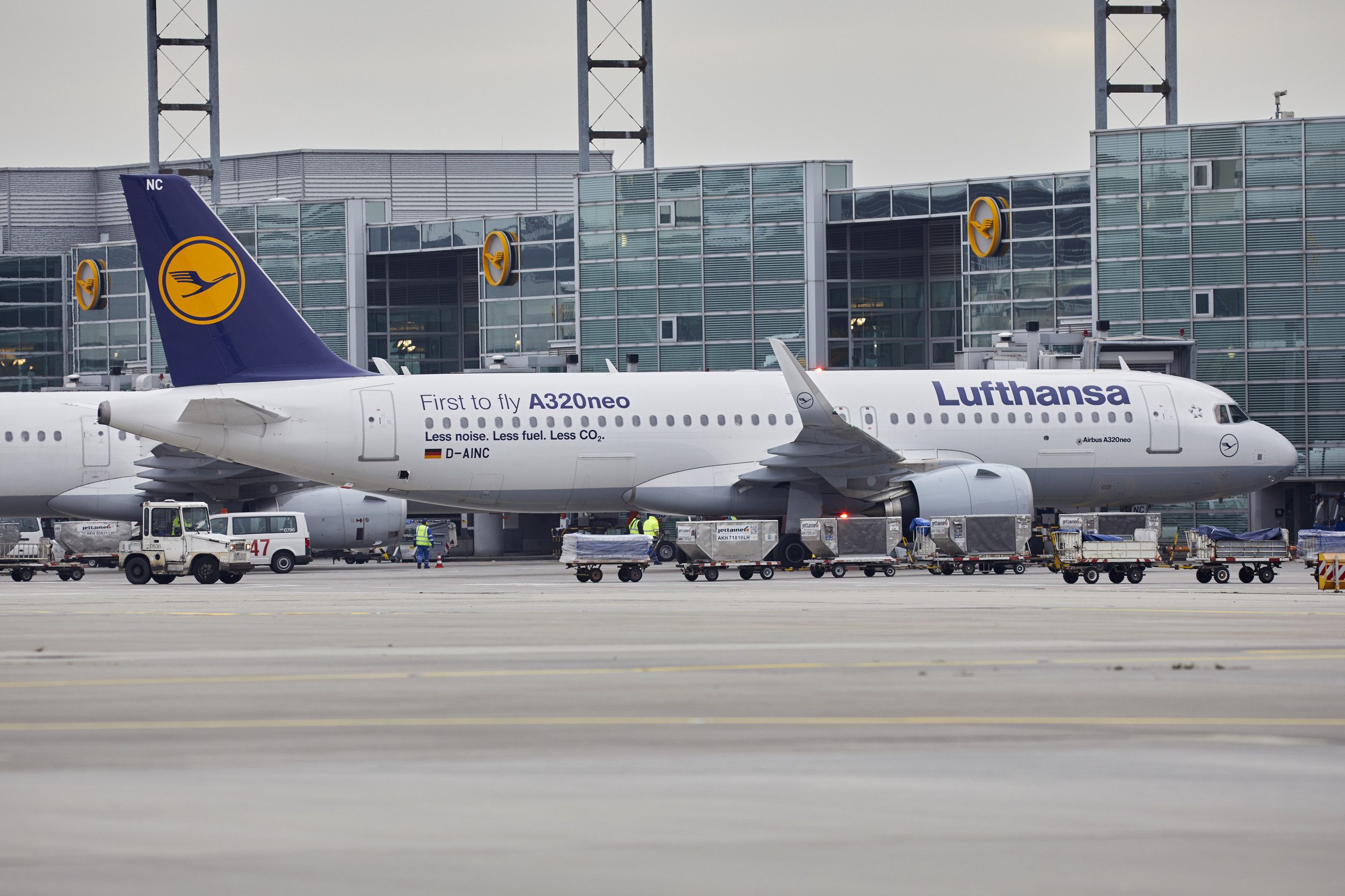
Lufthansa AirbusA320neo
It’s been a milestone without much fanfare except for a few tweets, but Pratt & Whitney has had something to celebrate recently: on January 25, the Geared Turbofan (GTF) has been in commercial service for five years on the Airbus A320neo. With Lufthansa, to be exact. In a two-part story, Airinsight looks back on these first five years, dictated by in-service troubles which all seemed to have been overcome by now. This is part 1.
The Geared Turbofan was conceived in the mid-nineties, but it has taken Pratt & Whitney until 2008 to formally launch the program that coincided with the launch of Mitsubishi’s MRJ-program. Pratt worked closely with its German partner MTU Aero Engines, which has designed the high-speed low-pressure turbine (LPT) a state-of-the-art core. But the GTF or Pure Power engine as it was also called had something extra: a fan drive gear system. The idea was simple: put in a gearbox to control the fan speed at a 3:1 ratio, and you can optimize the speed to forty percent of that of the low-pressure turbine and high-pressure turbine (HPT).
Scale model of the GTF’s powered gearbox that at a 3:1 ratio reduces the speed of the fan. (Richard Schuurman)
P&W has developed a family of GTFs: the PW1100G-JM for the Airbus A320neo-family rated at 24.000-33.000 lbs. of thrust, the PW1200G for the Mitsubishi MRJ/SpaceJet at 15.000-17.000 lbs., the PW1400G-JM for the Irkut MC-21 at 28.000-31.000 lbs. (in size almost identical to the PW1100G-JM), the PW1500G for the Bombardier C-series/Airbus A220 at 19-25K lbs., the PW1700G for the Embraer E175-E2, and the PW1900G for the E190-E2 and E195-E2 at 14.000-17.000 lbs. Only the 1100, 1500, and 1900-series have entered commercial service while the others are in various stages of aircraft flight and certification tests.
Almost five years after its entry into service, P&W reports a technical dispatch reliability rate of 99.98 percent for the PW1100G-JM. “Thanks to upgrades completed in close coordination with our customers in 2020, GTF engines for the A320neo family are now delivering industry-leading reliability,” the December 2020 press release quotes Carroll Lane, president of Commercial Engines.
The first issues
‘Upgrades’, there have been some. While the geared turbofan concept has never been in doubt and has performed reliable, a raft of other issues has plagued the engine, which actually is called International Aero Engines PW1100-JM (like the PW1400-JM) because of the collaboration between P&W, Japanese Aero Engines Corporation (JAEC), and MTU Aero Engines.
Even before the GTF entered service, there had been the infamous ‘bowed rotor’ in 2015. Irregular cooling led to the bowing of the high-pressure compressor (HPC) shaft that caused fan blades to potentially rub against the HPC case. It took a special motoring start-up procedure, a different build, plus software updates to get to grips with the issue. By then, Qatar Airways had become so annoyed that it walked away from an order for fifty GTF-powered A320neo’s. It later ordered A321neo’s instead – with CFM LEAP-engines. Qatar’s decision made Lufthansa the first operator of the GTF in January 2016.
Two of the GTF’s biggest operators, IndiGo and GoAir, ran into other problems quite soon after starting operations with their neo’s from March 2016. They experienced numerous in-flight shutdowns. Detailed examination showed a surprising cause: cooling holes inside the combustor chambers were clogged and showed serious distress and corrosion, with the loss of protective coating and even burn through. In a January 2017 incident on an IndiGo neo, a stud within the combustor broke loose and caused internal damage. Further analysis identified the humid environment and even polluted air over India as contributing factors to causing a 25 percent degradation of the combustor chamber.
As a result of these issues, especially in 2017 and 2018, IndiGo and GoAir have been forced to frequently ground their neo’s as aircraft became inoperable and spare engines were unavailable. Engines were placed under borescope inspection intervals every 350 flight hours while Pratt & Whitney redesigned the combustor to make it more durable (by 5x). It took until mid-2018 to be completed but even longer before the updates became available on new engines or as a retrofit, causing severe disruptions in engine deliveries to customers and Airbus.
Borescope pictures showing serious corrosion and burn-through in a GTF on an IndiGo A320neo in January 2017. (DGCA)
Seal troubles
GTF issues didn’t stop here. The number 3 bearing had to be redesigned in 2017 from the lift-off air seal to the dry-face carbon seal after it was found that metal parts had premature wear and got through the seal and into the oil system with oil leakage. The bearing was also identified as the cause of vibrations, a P&W spokesperson told the author in 2018. In the first 1,5 years of GTF operations until August 2017, there had been 77 premature engine removals due to number 3 bearing distress and 26 to combustor chamber distress, a report from India’s Directorate-General for Civil Aviation (DGCA) on a GoAir bearing incident said.
In 2018, a modified version of the rear rotor hub knife-edge seal in the high-pressure compressor caused more in-flight shutdowns and aborted take-offs. Regulators requested additional checks and inspections of both the HPC and second-stage HPT vanes. Initially, P&W referred back to the original design which performed more reliably while at the same time working on a modified seal.
The low-pressure turbine (LPT) has also been subject to numerous Airworthiness Directives. One in 2018 featured the number one and three-stage disks after manufacturing defects were found. A modified version was available from early 2019.
Other ADs addressed third-stage blade failures and fractures, some of which occurred from 2017 until February 2020 when debris from the combustors and a fractured turbine piston seal damaged the blades. Regulators qualified it as an unsafe condition that could result in the loss of the airplane. A November 2019 notice of proposed rulemaking featured third-stage blade failures, requiring the replacement of blades within ninety days and forcing P&W into a blade redesign with a different alloy. New blades have been installed on all new engines and as an extensive retrofit since 2020.
In June 2018, an AD was issued after corrosion on the HPC front hub, causing a potentially dangerous situation if not addressed beyond 4.400 cycles, although this issue has been seen on other engines as well.
In September 2019, an upgrade was done on the main gearbox after fractures were found in the integrated driver generator oil pump drive gear shaft assembly. Back in 2017, metal parts from the gearbox had already been detected by chip indicators, although in a specific GoAir incident an assembly error has been the cause. In other cases, high-cycle fatigue had caused multiple in-flight shutdowns, after which regulators responded by limiting operations and requesting inspections. It was managed through engine software fixes and an extensive retro-fit program.
The P&W GTF has fan blades of an aluminum alloy. This is a PW1900G on an Embraer E190E2. (Richard Schuurman)
Turning the corner
The good news is that no further ADs for the PW1100-JM and 1400-JM have been issued since August 2020, which is an indication that the GTF has finally reached a state of maturity and reliability.
In an investor’s call back in May 2019, IndiGo quoted technical dispatch reliability of 99.85 percent “which is actually 100 percent comparable to other engines.” Chief Operating Officer Wolfgang Prock-Schauer said: “In terms of in-flight shutdown rate, it has been reduced by half and is now much below the international required standards. So, we are absolutely confident that all these measures which have been initiated by P&W will show results.” By October that year, the in-flight shutdown rate at IndiGo had come down to 0.01 percent, five times better than the requirement of 0.05 percent from the FAA.
Even India’s DGCA, which since 2016 has taken a hard stance against the GTF-issues and forced airlines to ground neo’s on numerous occasions, is seeing light at the end of the tunnel. Having witnessed no issues on modified and new engines with the latest specs and following a request from IndiGo, DGCA in January this year relaxed the extended diversion time operations (EDTO) from sixty to ninety minutes. This allows neo-aircraft to operate on a single-engine ninety minutes from the nearest diversion airport. DGCA dictated that all engines are from the latest specifications. The GTF-fleet in India now has surpassed 180 aircraft and accumulated over two million flight hours. That’s about a quarter of 7.9 million flight hours done worldwide.
Another positive note is that the GTF has fully lived up to its expectations as far as fuel burn improvements are concerned. In 2018, P&W reported an average better specific fuel burn of sixteen percent compared to previous generation engines but now quotes “up to twenty percent”. The A320neo-family has seen sixteen percent, while the Embraer E2-family that entered service with Wideroe in June 2018 is recording 17.3 percent. On the Airbus A220-family, a 21-23 percent improvement has been demonstrated. Nitrogen oxide (NOX) emissions are fifty percent better while the noise footprint of the GTF is 75 percent smaller based on a 75 dBA contour. Hearing a GTF-powered aircraft take-off or pass overhead indeed makes a significant difference, with the lower fan speed giving the engine a lower pitch sound.
Open doors on the starboard PW1500G on the first SWISS Bombardier CS100, seen at Farnborough 2016. (Richard Schuurman)
PW1500G uncontained failures
The second GTF-version to enter service was the PW1500G on the Bombardier C Series/Airbus A220, with SWISS in June 2016. It has had its share of issues too. Before the type was certified, a Bombardier CS100 suffered an uncontained failure during ground tests in May 2014 which was caused by the failure of a bearing oil feed tube line following insufficient cooling.
SWISS, Korean Air, and airBaltic have all suffered from problems. In 2017, airBaltic’s Martin Gauss told the author at the Dubai Airshow that extra inspections and combustor issues forced his airline to swap engines between 200 and 1.000 flight hours and complicated operations. airBaltic even briefly suspended C Series operations in October that year as inspections were done. Upgrades to the combustors are underway in a similar fashion as the PW1100G-JM family.
More serious were two uncontained failures with SWISS in July and September 2019. In both events, the LPC stage 1 rotor disk disintegrated on the number one PW-1524G-3 when the Airbus A220-300s were climbing to cruise altitude. In an October 2019 AD, the FAA requested initial and repetitive inspections of the LPC inlet guide vanes and rotor 1 disk while reducing maximum thrust to 94 percent when over FL290. In response, SWISS immediately grounded its A220-fleet but other operators kept flying as their engines were of a different spec. Because of similarities in type design, the AD also extended to the PW-1900 family on the Embraer E2, although no issues have been reported.
Following two other in-flight shutdowns in October 2019 with SWISS and in February 2020 on a PW1521G with airBaltic and after further investigation by P&W, the root cause was found: an acoustic resonance coming from LPC vanes schedules damaged LPC stage 1 rotor and resulted in a disk failure. As a first step to eliminate the problem, the software of the Full Authority Digital Engine Control (FADEC) system on the PW1500G was updated to alter the vane schedule. However, after digging further into the issue, it was discovered that the ‘acoustic coincidence’ passed over the 2.5 stage bleed-valve duct cavity from the stage 3 to stage 1 rotor, FlightGlobal reported on March 5. This resonance caused the cracking in the stage 1 rotor that resulted in bending of the blades and, in the end, rotor failure. That’s why the bleed-valve ducts will be redesigned.
It’s unconfirmed if these issues were related to an earlier uncontained failure in December 2018 on a Korean CS300. Despite these events and issues, the PW1500G has reached good reliability. Airinsight has learned that at a 99.9 percent dispatch reliability rate is almost matches its PW1100 sisters.
Other issues for which regulators issued AD’s for both the PW-1500G and PW-1900G series were front hub wear and leakage from a fuel oil cooler, resulting in low oil pressure. An engine flameout occurred on a PW1200G on the Mitsubishi MRJ90 during a test flight in August 2017 out of Moses Lake, but this seems to have a one-off incident. No problems have been reported with the PW1400G on the Irkut test fleet.
P&W – previously owned by United Technologies (UTC), now Raytheon – has never publically disclosed the specific costs coming from the various GTF issues, redesigns, and compensations. They must be hidden within the “charges resulting from ongoing customer contract matters” in UTC’s annual reports, with $142 million in 2015, $184 million in 2016, and $385 million in 2017. No figures are mentioned in subsequent reports. Tech issues, the necessary upgrades, and production delays (especially with the aluminum-titanium fan blades, solved by the opening of a third site) have severely impacted production at Airbus and Bombardier. The sight of dozens of parked neo’s and C-Series ‘gliders’ without engines are only a few years ago, as are Airbus’ critical remarks to P&W to “get their act together.”
In part 2, we look at where the GTF is now and how airlines rate it. Plus what could be in store for the Geared Turbofan.
Views: 270
A new, most advanced reactor system, including patented energy production and renewal, to produce efficient and sustainable energy for aviation vehicles.