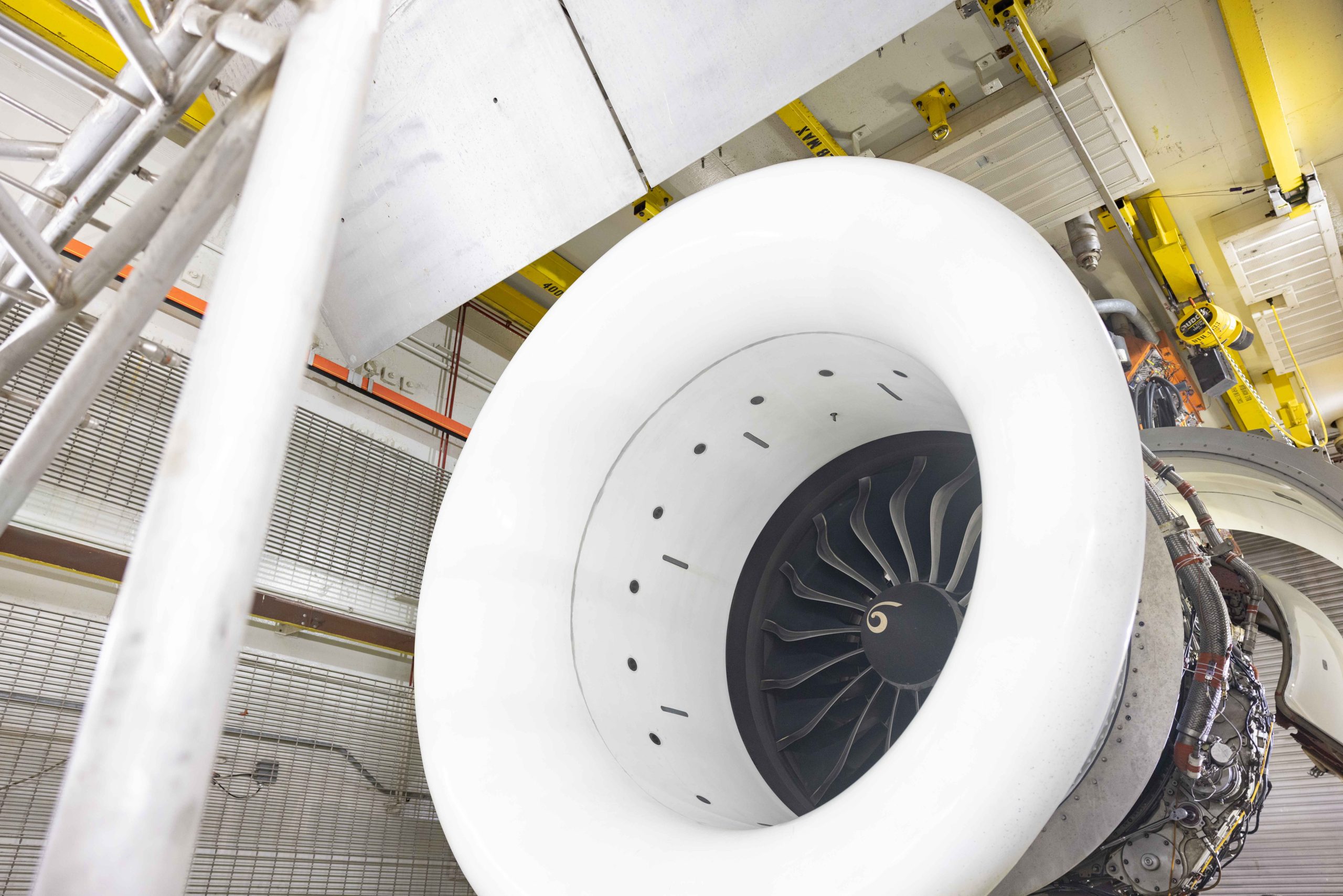
LEAP Dust Ingestion 0091 1
GE Aerospace and partner Safran have been successful in replicating the circumstances that have affected the durability of the CFM LEAP engines, including high-pressure turbine (HPT) blades and fuel nozzles. Specifically, the effects of sand dusting on the engine are now better understood. Thanks to this, they think they now have a better understanding of the problems and know how to solve and prevent them. CFM gets a better understanding of sand dusting on the LEAP.
The durability issues with the LEAP were raised during a Paris Airshow media presentation on Saturday of GE Aerospace and CFM in Paris. While updates of the RISE open rotor technology demonstrator were offering new insights, the leadership of CFM took considerable effort to go into the success of the LEAP as well.
CFM President and CEO, Gaél Méheust, said that the LEAP is at 92 a percent days flown ratio, which brings it to pre-pandemic levels. On May 31, there were 2.713 engines in service on the Airbus A320neo-family and Boeing MAX. LEAP-1A flight hours on the Airbus fleet exceed 22.8 million and flight cycles 11 million on 1.504 engines. The MAX fleet of 1.208 engines is at 10.5 million flight hours and over four million cycles. The LEAP has reached 30 million flight hours the fastest of any commercial engine.
CFM has a backlog of over 10.000 LEAPs, including over 1.000 that have been ordered or committed by COMAC for the -1C variant that powers the C919. The -1A has a 60 percent market share on the Airbus A320neo family and a 55 percent share on the A321XLR, which is currently in the flight-test program leading towards certification in 2024/2025.
While reliability levels after seven years in service exceed those of the CFM56, the LEAP has had its issues. GE Aerospace already detailed the HPT and nozzle issues in March during its Investors Conference. Karl Sheldon and Jérome Morhet, both executive vice presidents at CFM, confirmed that higher wear has caused more issues than were anticipated. New HPT blades and nozzles are now expected to be available on new engines in the latter half of 2024 and as a retrofit during shop visits a short while after that. This is slightly later than what GE said in March.
Higher wear in hot and harsh environments
Like its competitor Pratt & Whitney and the Geared Turbofan, CFM has seen higher wear in regions with hotter and harsh environments, like the Middle East and India. Sheldon was unwilling to compare the issues but said that GE and CFM have taken a lot of effort to understand what is causing the wear.
“Designing, testing, and validating the durability of the blade through our dust testing and the analytics that we have been maturing for years. The goal is to get the core durability to the same state that the CFM56 is today, that is the customer baseline for expectations in that region. That is what these new blades and nozzle will do,” said Sheldon. The LEAP has been run through its paces on a rig in Evendale (see main picture).
“In regards to the CFM56, the iterations to get to that level of durability over decades of development, we didn’t have the dust testing capabilities back then that we do now. Back then, we had to weigh and feel the blade and how it behaved over time. Now, we have been able to replicate very effectively what is happening in the field and what is coming out of the dust test. So the speed by which we will be able to come back to that problem has been cut back dramatically. So with this next iteration of durability changes to the blade and nozzle, we expect to hit that.”
Pushing the boundaries
That the LEAP hit problems in the first place, has a reason, Sheldon explained: “With LEAP, we pushed the boundaries of technology with the core and other parts of the engine. That’s where you get performance. With that change in the push in technology and performance come requirements for new blade-cooling technologies, new capabilities in predicting what that performance will be in the field.”
“We had to mature our component testing to get to that level and quite frankly, the first iteration wasn’t a perfect hit. Blade design and blade technology is one of the most advanced things we do. We shot for it and didn’t hit the mark, so now with the dust testing coming to maturity to validate that, we think we have converged on where we need to be.”
Views: 108