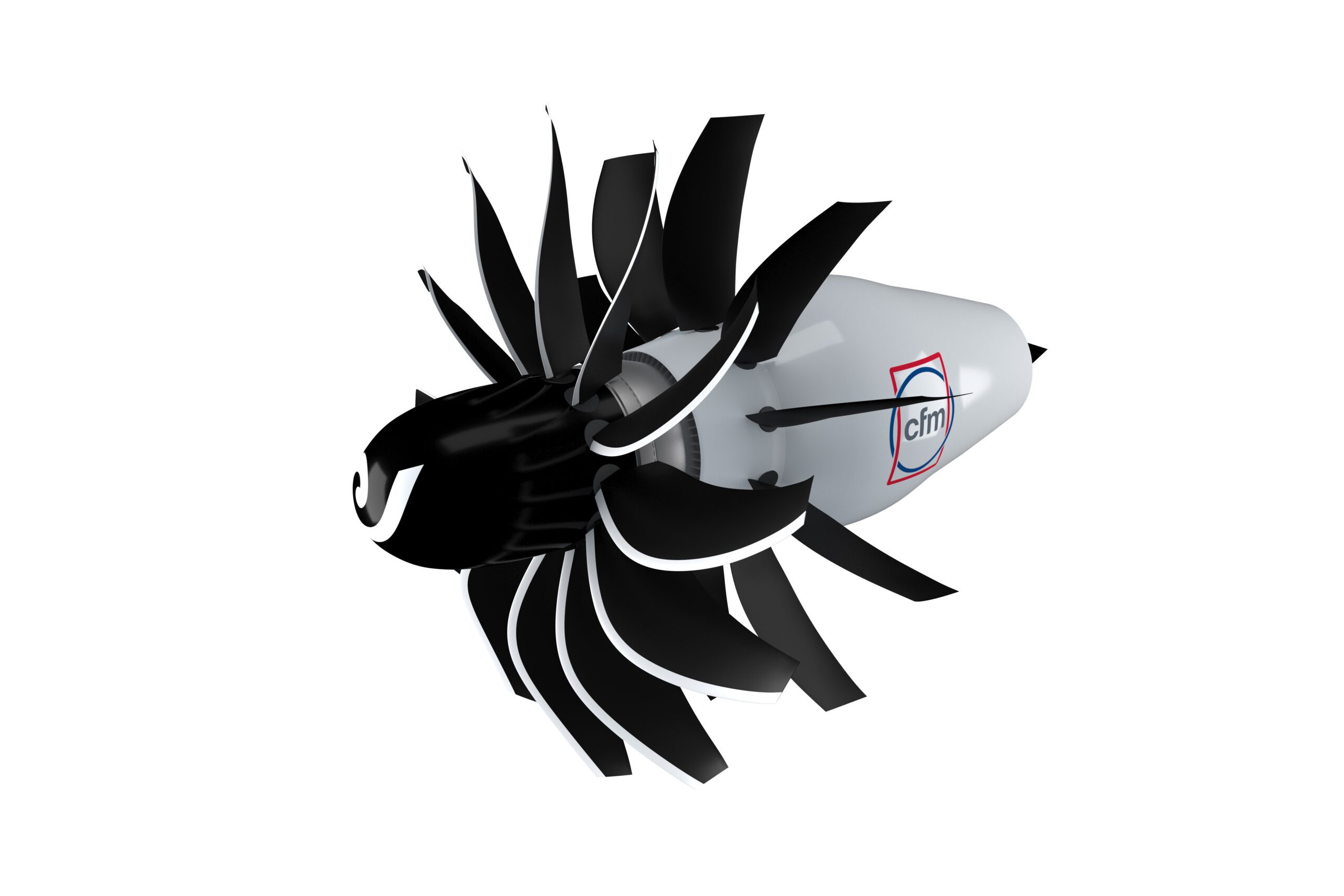
02 CFM RISE Program Open Fan scaled
The CFM International RISE (Revolutionary Innovation for Sustainable Engines) Technology Demonstration Program was launched on June 14, 2021. Program goals include reducing fuel consumption and carbon dioxide (CO2) emissions by more than 20% compared to today’s most efficient engines, as well as ensuring compatibility with alternative energy sources like Sustainable Aviation Fuels (SAF) and hydrogen to provide more sustainability benefits. All previous propulsion breakthroughs in efficiency were achieved by new technologies that allowed for a larger fan size and a higher bypass ratio.
CFM, the 50-50 joint-venture between GE Aviation and Safran, notes: “Although high bypass architectures can be seen in the form of turboprops on slower flying and shorter-range regional aircraft today, the open fan architecture to be demonstrated as part of the RISE Program is nothing like a turboprop engine. This advanced, new generation open fan architecture will be able to fly at the same speed as current single-aisle aircraft (up to Mach 0.8, or 80 percent the speed of sound) with a noise signature that will meet anticipated future regulations. CFM RISE PROGRAM Revolutionary Innovation for Sustainable Engines.”
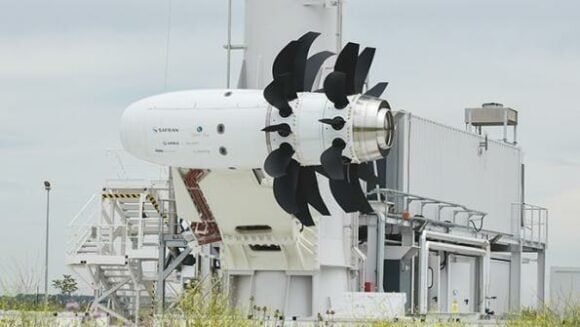
Â
The RISE demonstrator engine (next image) will deliver 30.000lb of thrust, which is where the LEAP starts now. This suggests the initial focus is the single-aisle market. But scaling fan blades and core allows for growth. Notice the difference in the two images, the upper test engine has contra-rotating blades, but the RISE does not and appears to also have fewer stators than blades on the upper engine. Â
Commercial aviation has set a goal of achieving net zero emissions by 2050 and radical ideas need to be pushed to achieve that goal. Many industry watchers, along with several insiders, don’t believe the net zero goals are achievable. This is a fair view to take if one is thinking about what we know about engines and fuel today. Yet we can see that commercial aerospace has achieved incredible breakthroughs over its decades of existence. And continues to do so routinely. Being skeptical is understandable but betting against the industry isn’t the best strategy.
Ground tests by the mid-2020s
CFM plans to have a demonstrator engine for ground tests by the “mid-2020s”. To get more background on the RISE program we reached out to GE Aviation and Airbus. GE’s responses came from Arjan Hegeman, General Manager of Advanced Technologies for GE Aviation which is becoming GE Aerospace.
- Please walk us through the story of the CFM RISE program.
“Aviation is a long-cycle industry. The bigger the change in technology, the longer the lead time it takes to develop. The open fan engine design is a great example of this.”
“GE Aviation, which is becoming GE Aerospace, has been developing technologies to enable the open fan for decades, beginning with the 1970s Quiet Clean Short-Haul Experimental Engine (QCSEE) demonstrator with NASA, the first high-bypass geared turbofan engine. In the mid-1980s, we developed the GE36 or Unducted Fan (UDF), and Safran Aircraft Engines, then Snecma, was part of the development and testing. The GE36 flew on a Boeing 727 and on both a DC-9 and an MD-80, with the latter aircraft flying at the 1988 Farnborough Airshow.” (see picture below) GE was not alone in exploring the open rotor, as Pratt & Whitney-Allison also tested their propfan concept.Â
“Since then, we haven’t sat still, continuing to evolve the open fan design. In the 2000s, GE and Safran conducted significant aero and acoustic testing that advanced the technology. In 2017, Safran Aircraft Engines successfully performed a Counter-Rotating Open Rotor (CROR) engine ground test as part of the European Clean Sky initiative, demonstrating a 15% improvement in fuel consumption and CO2 emissions compared to today’s most efficient engines. GE’s Avio Aero business was part of that program.”
“As a result of these tests, we demonstrated that an open fan configuration can achieve improved noise levels even relative to today’s state-of-the-art engines, enabling us to address current and anticipated noise regulations (Chapter 14). We have also been able to reduce both the complexity and weight of the engine while maintaining significant performance benefits.”
“GE has further advanced the state of the art by introducing the current single-stage, variable pitch open fan design with stationary outlet guide vanes. The outlet guide vanes help direct airflow so the open fan can fly at speeds consistent with conventional turbofan engine architectures while improving energy efficiency at noise levels below current generation turbofans.”
“We believe the time for an open fan is now, and that’s based on research and technology that has matured for more than 40 years. GE and Safran in June 2021 proudly unveiled plans for the CFM RISE technology program, which will demonstrate in flight a series of new propulsion technologies such as the open fan for a future, next-generation single-aisle aircraft application. The goal of the RISE Program is to achieve a more than 20% improvement in fuel efficiency compared to today’s engines. The open fan design is key to exceeding the 20% target.”
Climate change drives urgency
- Open rotors have always been big on promised fuel burn improvements but never got to market – why is this time different?
Hegeman continues: “The open fan architecture was originally designed in response to rising fuel prices, which have fluctuated over time. What makes today different is that climate change will continue to drive and increase the urgency to introduce propulsion systems that get the world to more sustainable flight. And these kinds of disruptive technologies that revolutionize aircraft engines are needed to truly reach our net-zero ambitions.”
“The other difference from before is that GE has developed very advanced technologies, both in our engine designs as well as in our design tools, which have enabled our engineers to advance the state of the art beyond what was previously believed to be impossible. The big breakthrough from this is that we now have an open fan with the same efficiency benefits, but at very low noise levels and smaller dimensions to make it easier to integrate with the airframe.”
GE and our partners are putting our best technology — like the open fan engine architecture — on the table towards reducing CO2 emissions for a more sustainable aviation industry.”
- A 20% improvement is amazing – how much more can this approach squeeze out?
“An open fan architecture enables a much higher bypass ratio and, as a result, delivers much higher propulsive efficiency. Achieving 20% better fuel efficiency has the potential to be the single greatest generational improvement in fuel efficiency that we’ve ever achieved.”
“Our open fan architecture demonstrator is also the first iteration of a new engine approach. Our current architecture of commercial turbofan engines started with the GE90, which entered service in 1995, and has since evolved and improved through the GEnx, the CFM LEAP, and now the GE9X engines. Each new engine introduction has significantly improved fuel efficiency compared to its predecessors through the introduction of new technologies such as composite materials.”
“Open fan resets this baseline. It moves the overall fuel efficiency up with a generational step-change improvement. Clearly, just as the GE90 was the start of a large family of engines, each improving upon its predecessor with the insertion of new technologies, the CFM RISE technology demonstrator is only the beginning.”
“Developing more fuel-efficient engine technology that reduces fuel consumption and CO2 emissions is also critical for the limited supply of alternative fuels. More efficient engines consume less fuel per flight compared to the engines they replace. Open fan, hybrid electric, and other technologies in development are being designed for compatibility with 100% SAF and hydrogen. All our engines can operate with SAF today, which is certified in the industry up to a 50% blending limit and can reduce lifecycle CO2 emissions for fuel production and distribution up to 80%. 100% SAF will further reduce lifecycle CO2 emissions. Hydrogen has the potential to eliminate CO2 emissions during flight, and as part of CFM’s collaboration with Airbus on the ZEROe program, our engineers will study the effect of hydrogen contrails and nitrogen oxides (NOx).”
- It seems your team has started to solve the noise challenge – what about blades spinning in the open? I’m thinking here about a blade-off situation.
“GE’s commitment to safety is uncompromising. With the development of open fan engine architecture, we have and will continue to work closely with the airframers and global authorities to finalize the design and develop a regulatory framework for the certification of an open fan engine. We are also confident based on our decades of experience with introducing ever-advancing technologies, including our industry-leading composite blade experience, which first entered service with the GE90 engine in 1995. GE now has more than 100 million engine flight hours with composite blades.”
- The engine will be tested on an Airbus A380 – why that aircraft? Why not the GE 747 testbed?
“We are very proud to be partnering with Airbus and Boeing in demonstrating the revolutionary technologies for the aviation industry to get to our 2050 emission ambition. Advanced new technologies like open fan make partnering with airframers even more important for aircraft and propulsion integration.”
“These efforts include a partnership between Airbus and CFM International to conduct flight tests of a hydrogen-powered engine and the open fan. In partnership with NASA’s Electrified Powertrain Flight Demonstration (EPFD) program, GE is collaborating with Boeing to develop and fly a megawatt-class hybrid electric propulsion system.”
“These flying demonstrators are preceded by our own testing. The RISE Program includes more than 300 separate components, modules and full engine builds. These cumulate to ground tests of an open fan engine at our Peebles Test Operation in Ohio.”
Airbus’ role in the RISE program
- We asked Airbus: The CFM RISE open fan demonstrator engine will be tested on an A380 – is there a chance that a successful test might lead to a re-engine program?
Airbus: “No, this is a demonstrator. New propulsion technologies will play an important role in achieving aviation’s net-zero objectives and demonstrators are key to evaluating, maturing, and validating all the different technology bricks that will enable us to reach our decarbonization goals. We already have/had a number of demonstrators in our R&T / R&D portfolios; The hydrogen ZEROe program is the most recent example (https://www.airbus.com/en/newsroom/stories/2022-02-the-zeroe-demonstrator-has-arrive).” (Also our story on AirInsight)
- Looking forward, can give us an of other potential Airbus aircraft that could use this engine?
“Airbus and CFM are collaborating on a joint Flight Test Demonstrator program to test CFM’s Revolutionary Innovation for Sustainable Engines (RISE), open fan propulsion technology, and architecture, that could improve aircraft and engine efficiency. The research dedicated to engines (propulsion systems) is part of the development of a mix of technological solutions to foster aircraft efficiency and overall reduce fuel consumption to reach our net zero emission ambition by 2050, therefore this engine is not destined for any other usage other than this. The A380 is a unique quadruple engine carrier and the perfect candidate for a flight test technology demonstrator.” (aeroTELEGRAPH reported from Farnborough that the A380 demonstrator will not be MSN001 which is being used for ZEROe tests, but another unidentified frame, with Airbus as the source)
- How long will this test period be?
“Airbus and CFM will work together to detail the exact list and sequence of ground and flight testing to be performed in the second half of this decade. We anticipate approximately 100-200 flight hours will be required to understand and refine engine performance, acoustics, operability, and control.”
- Looking forward, can give us an idea about power ratings and potential aircraft that could use this engine?
“Through CFM’s RISE Program, we are demonstrating advanced technologies in a single-aisle aircraft-sized propulsion system. Note, just like the UDF in the 1980s demonstrated the feasibility of composite fan blades, which since then, have been used in every thrust class in GE and CFM engines, the RISE Program technology suite will also find its way into future generation engines of all thrust classes.”
- How long will this test period be and when might we see the engine certified for commercial use?
“GE and Safran Aircraft Engines plan to spend this decade on technology development and maturation and have various flight tests planned for hybrid electric systems, hydrogen combustion, and other CFM RISE Program technologies like open fans. Flight tests will help prove our technologies, leading to engine product launches. The open fan and other advanced new engine technologies could potentially enter commercial service in the 2030s, depending on airframer strategies.”
Views: 315
It seems RISE single prop is actually mechanically a simplification of the open rotor concepts of the eighties. Reducing weight and noise. Also going after a prop puller instead of pusher configuration reduces a lot of cooling and noise challenges.
Therefor for me it is a far more confidence building direction than the previous concepts. If we have to surrender some speed on shorter flights that’s a price we need to pay IMO..
Embraer using it on their new turbo prop configuration could further improve efficiency. winning back the energy wasted in the swirl of the wake of a normal TP, by redirecting the props airstream straight aft again, could improve sfc by about 4-5%.